What the INK is going on?
The Role of Ink Measurement in Flexographic Printing
Have you ever been on a press run that just isn’t going to plan? Maybe you’re struggling to achieve the right color, dealing with foaming ink pans, or constantly stopping to clean your plates. If you’ve ever thought, “What the ink is going on?”—you’re not alone.
Ink accounts for about 3-4% of total package costs and plays a massive role in print quality and press efficiency. Many common pressroom issues can be traced back to ink inconsistencies, but taking a proactive approach to ink measurement and monitoring can prevent issues before they start. By consistently tracking key ink parameters, printers can avoid print defects, reduce downtime, and optimize ink usage.
What to Track and How to Track It
1. Ink Viscosity: The Key to Print Performance
Managing the viscosity of solvent- or water-based inks is crucial for achieving consistent print quality. Ink viscosity affects both press performance and print results by influencing:
- Press Performance: Ink usage, drying speeds, solvent retention, ink flow, and anilox roll performance.
- Print Quality: Smooth ink laydown, dot gain, trapping, color strength, adhesion, and color accuracy.
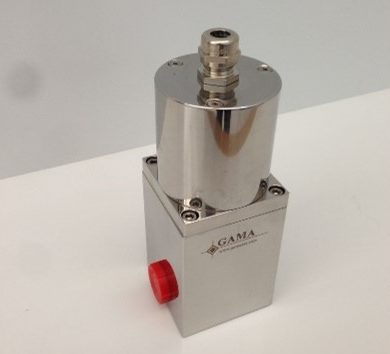
Without accurate ink measurement, viscosity fluctuations can lead to mottled prints, poor trapping, and inconsistent color strength. To maintain proper viscosity levels, printers can integrate viscometers directly into their ink distribution systems. GAMA’s viscometers, for example, continuously monitor and regulate viscosity, ensuring precise ink flow throughout the press run.
BING Tip: Maintain ink viscosity within the range determined during press optimization and characterization. Typical ranges vary by application, but these are our recommended starting points:
- Printing flexible packaging with solvent-based inks: 22-26 seconds in a #2 Zahn cup
- Printing on paper with water-based inks: 18-24 seconds in a #2 Zahn cup
2. Ink Contamination: Preventing Costly Defects
Even in the cleanest pressrooms, debris and foreign particles can enter the ink system, causing major issues. Contamination can lead to frequent plate cleaning, hickeys in the printed image, or even worse—scratched or damaged anilox rolls.
Filtration systems provide a simple but effective way to enhance print quality and protect valuable equipment. Tools like the Superflo® Filter and megaMAG™ from Graymills help remove contaminants before they cause defects. Regular ink reservoir checks can also help detect contamination before it impacts the final print.
BING tip: You’d be surprised what you might find in your ink reservoir, or in other areas of your pressroom. We’ve seen metal debris in the following components:
- Incoming solvent
- Incoming fresh ink
- Pressroom rags
- Substrate
- Old plumbing pipes and delivery truck pipes
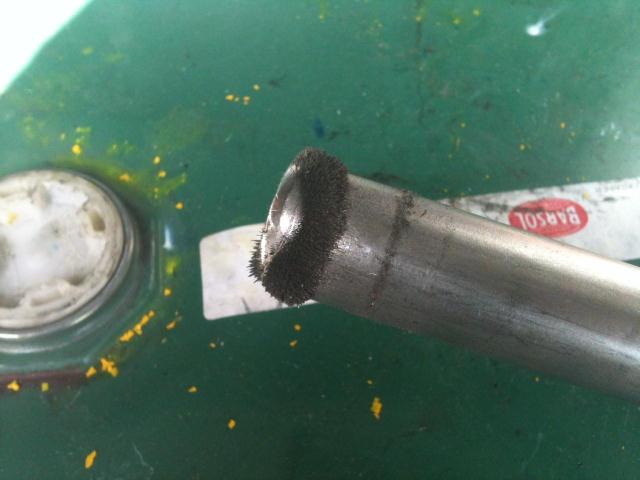
3. Ink Volume Usage: Tracking for Efficiency
Estimating ink usage can be a challenge, especially when dealing with specialty color matches. Running out of ink mid-job forces an unnecessary press stop, affecting production efficiency. Real-time ink measurement allows printers to track consumption, ensuring they have the right amount of ink for every run.
The CCS One from GAMA provides real-time monitoring of ink usage, alerting operators at preset thresholds. This system not only prevents press interruptions but also stores data to uncover usage trends, improving future estimations and reducing ink waste.
An effective ink management system isn’t just about reducing waste, it’s about improving overall efficiency and print quality. Investing in the right ink quality control tools with Bingham and monitoring best practices can set your operations up for long-term success.
Need help optimizing your ink management? Contact our expert Flexo team to find the right ink measurement solutions for your pressroom.